- Products
- Segments
- Newsroom
- Tools and Resources
- Sustainability
- We are Nexans
- Search
- Contact us
- Compare
- Sign in
Make development possible
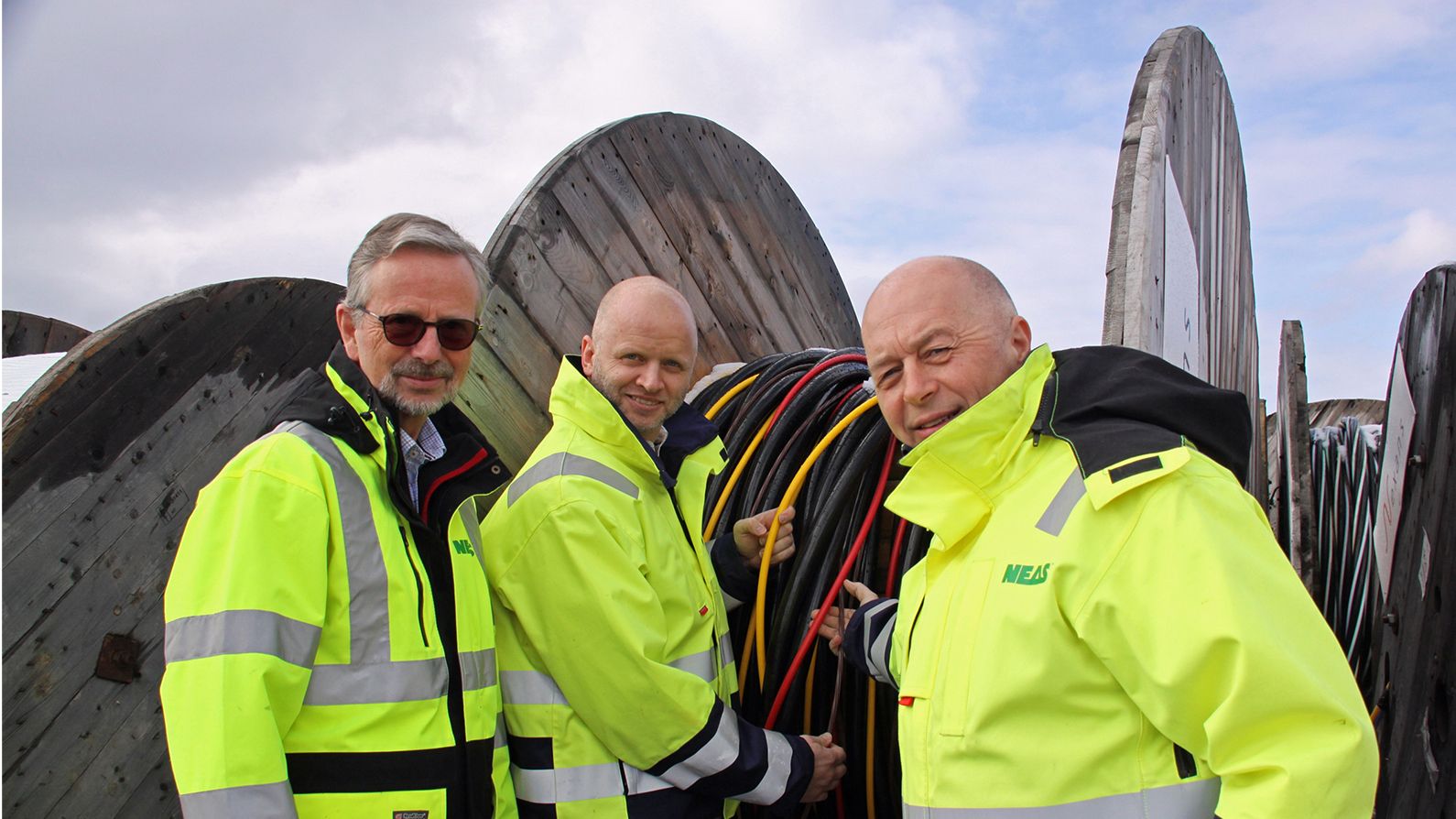
-
LOCATIONNorway
-
PARTNERSHIPUtility
-
SolutionSmart cables
It’s the very backbone of the whole organization. NEAS gives high priority to far-sightedness and viability to provide the requisite infrastructure to the general public.
“As an organization we take our social responsibility seriously. Shouldering this responsibility requires us to take a farsighted approach to our work,” says Tormod Stene, Division Manager, Grids, Nordmøre Energi AS (NEAS).
Important infrastructure
Kristiansund Municipality and four other surrounding municipalities are majority owners of NEAS, which means that the power plant must provide infrastructure to roughly 26,000 grid customers.
“ The owners are committed to being a responsible operators of a socio-economically important infrastructure. At the same time, it’s our duty to ensure that people living in sparsely populated areas have access to this same infrastructure,” Stene says.
Ensuring viability
NEAS is responsible for selling energy, electricity and broadband in its concession area. At present, NEAS provides broadband services to 16,000 customers.
“Broadband is our fastest growing business segment,” Stene says.
Our organization has long seen a need to coordinate our various business areas. Whenever we excavate a trench, it’s crucial for us to fill it with options that go beyond today’s needs. This helps ensure the viability of our cabling systems.
“Both price and quality are important to us. This is one reason why we’ve been using Nexans’ smart cables since 2007,” he says.
Filling the winding spaces
Head of Department Arnt Viktor Hansen, who is in charge of planning the development of the grid structure, works closely with Kjetil Hansen, Head of the Broadband Section.
“Substantial investments can be saved by laying a product that contains multiple functions. We can cut the number of reels we use by two-thirds for instance,” Arnt Viktor Hansen says.
Nexans’ O-cable (aka ‘smart cable’) takes advantage of the winding spaces within the braided power cable. This makes it possible to integrate a power cable, empty conduits, tubes with pre-blown fiber orcopper wire into one and the same product. Customers can then add products that must be wound onto the cable to meet the needs of the individual cabling systems.
“We’ve chosen to lay conduits in all three winding spaces. Today, we blow fiber into one of them, while keeping the other two open for future use,” says Kjetil Hansen referring to NEAS’s vision to enable development.
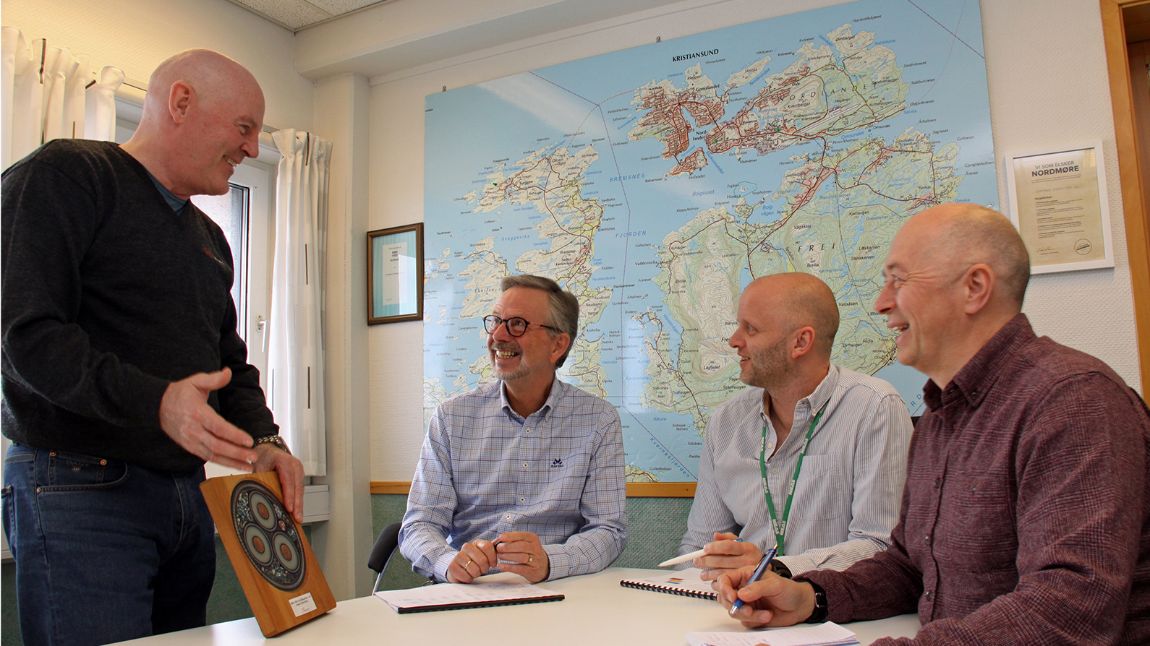
Consumer friendly
The various NEAS divisions share the cabling costs. This also means that they share the trenching costs.
“The cable-routing costs far exceed the cost of the materials. This means digging the narrowest trench possible and filling it with much material as possible,” Arnt Viktor Hansen says.
By gathering the various functions in the smart cable, they reap substantial financial benefits as well. The pulling costs are divisible by the number of integrated cables and tubes that are laid.
“It’s a matter of reducing the end-user’s price,” he says.
Prevents damage
Infrastructure viability is another aspect of the need to allow for future developments. This means physically ensuring that the infrastructure is capable of meeting more than just current needs, and that the infrastructure is high quality, and has a long service life as a result.
“We know that Nexans uses a stiffer grade and bigger conduit dimensions than its competitors. This ensures that it will be easier to blow fiber into laid pipes in the future,” Kjetil Hansen says.
He adds that because the conduits are well protected in the winding spaces, the likelihood of damage is reduced, both during cable-laying and once the product is underground. Having the right conduits in the winding spaces of the cable also reduces friction by about 30% when pulling in pipes, thus reducing the need for pulling power.
“ We haven’t experienced any damage to Nexans’ O-cables,” he says.
Training course
Every year since 2010, NEAS has laid more than 10,000 meters of Nexans’ 24 kV O-cable, in different cross-sections. For 1 kV cables, the total volume approaches roughly 250,000 meters since the start-up.
“We haven’t received any complaints about material defects,” Stene states.
The only challenges encountered by the power plant were in the cable-laying process. To ensure the cable-laying quality, NEAS took advantage of Nexans’ expertise and organized training courses for contractors.
“We require any contractor who works for us to take a course in cable and reel handling. This has worked wonders,” Stene says.
He emphasizes that the quality of the cable-laying is crucial to the cabling system’s service life.
“It’s very helpful that Nexans makes its expertise available for the courses,” he says.
Our websites
Select your country to find our products and solutions
-
Africa
- Africa
- Ghana
- Ivory Coast
- Morocco
- North West Africa
- Americas
- Asia
- Europe
- Oceania