- Products
- Segments
- Newsroom
- Tools and Resources
- Sustainability
- We are Nexans
- Search
- Contact us
- Compare
- Sign in
Power cable hat-trick
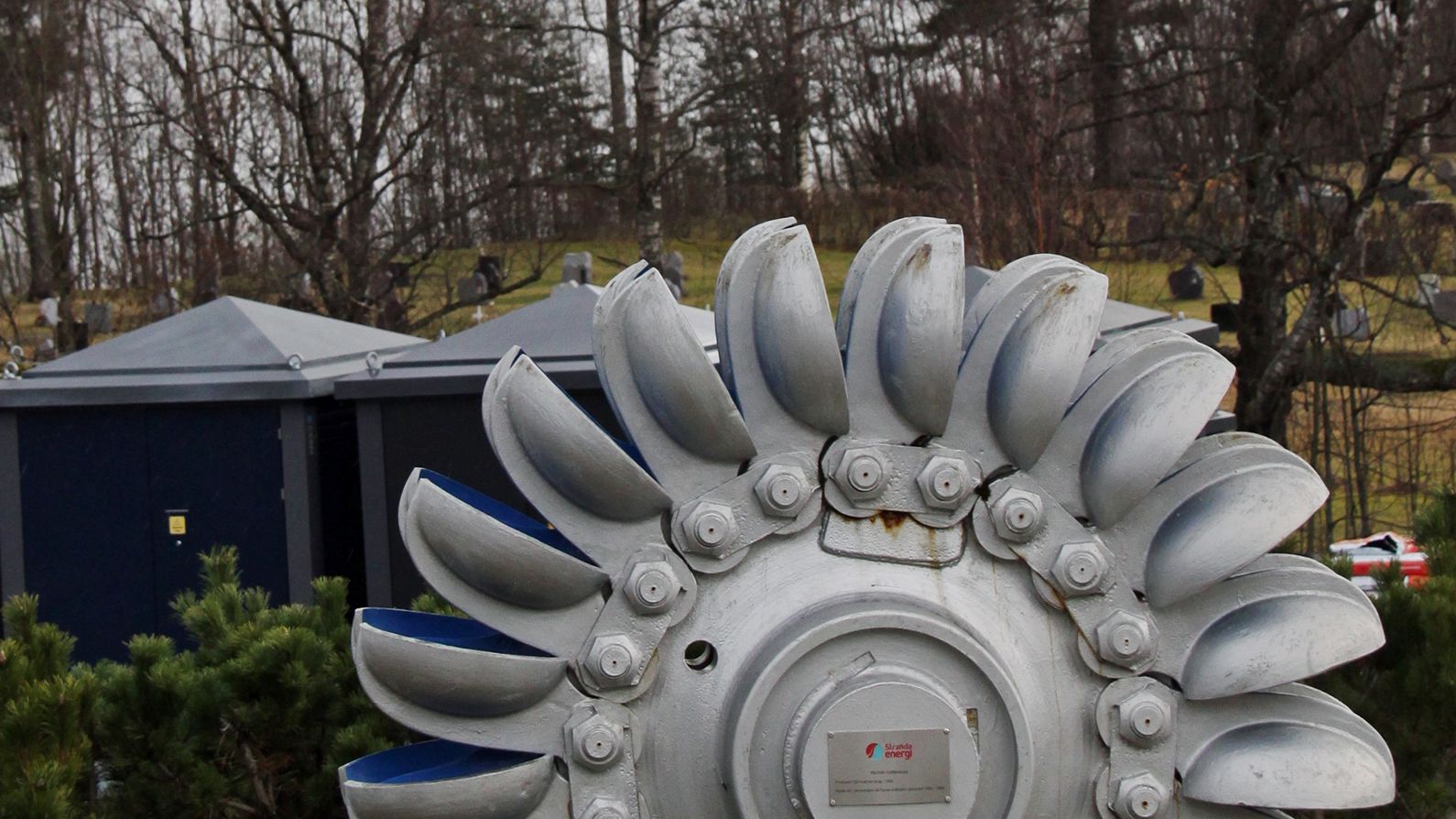
-
LOCATIONNorway
-
PARTNERSHIPUtility
-
SolutionSmart cables

In 2016, the power station was able to complete the laying of cable in the final construction stage of the new tunnel on county road 60 between Stranda and Hellesylt.
- We could pull lengths of up to
1,100 meters of TSLF-OF 24 kV,
3x1x240 mm² in a snap without
splicing, Terje Årdal states.
“ It frees up worktime. It gives us a huge advantage
because we’re so busy. ”
Terje Årdal
Grid Manager, Stranda Energi ASPicking list
Nexans’ smart cable (also called ‘O-cables’ or ‘hybrid cables) is an all-in-one solution. Just like when you buying a new car straight from the factory, you can pick and choose from a pick list.
“For the braided three-phase cable, we chose to integrate three conduits, one filled with pre-blown fiber,”explains Tore André Remme, Planning Engineer.
Saves time
Remme was tasked with planning the cable-laying in the tunnel. He is convinced that he will recommend using Nexans’ smart cable for upcoming projects as well. A new tunnel towards Geianger will be built as a landslide-disaster protection project.
“I’ve no qualms about starting on this smart-cable project,” he says, emphasizing the enormous benefit of the fact that multiple workflows are done at the same time.

“We also save time by being able to order one or more of the conduits in the cable with pre-blown fiber cable from the factory. We drastically reduces tunnel downtime, something we had to take into account when blowing fiber cable after traffic was allowed into the tunnel, or during the cable-laying phase with a lot of activity in the tunnel,” Remme says.
Cost-effective
Nexans Norway has developed a new generation of smart cable solutions that integrate power cable, empty conduits for blowing fiber, tubes with pre-blown fiber, or earthing lead into one and the same product.
“Being able to pull or lay a power cable, conduit, fiber conduit and possibly an earthing lead at the same time simplifies and speeds up the cable-laying process,” Årdal says.
He also emphasizes the enormous costs saved by reducing the amount of space needed in trenches.
“Instead of needing space for multiple functions, we can make do with only one integrated cable,” he says.
Fewer reels
The smart cable is delivered on a reel as an optimized supply according to the lengths and cross-sections specified by the customer.
“This way, we save time and money by eliminating time-consuming splicing operations and because there are no cut-offs. Also, the 24 kV cables are sheath-tested at 10 kV from the factory, which guarantees quality,” Remme thinks.
He also points out that transport costs are reduced by significantly reducing the number of reels compared to receiving separate reels of each of the various components.
“It also reduces the number of reels to cope with and return during the cable-laying phase,” he says.
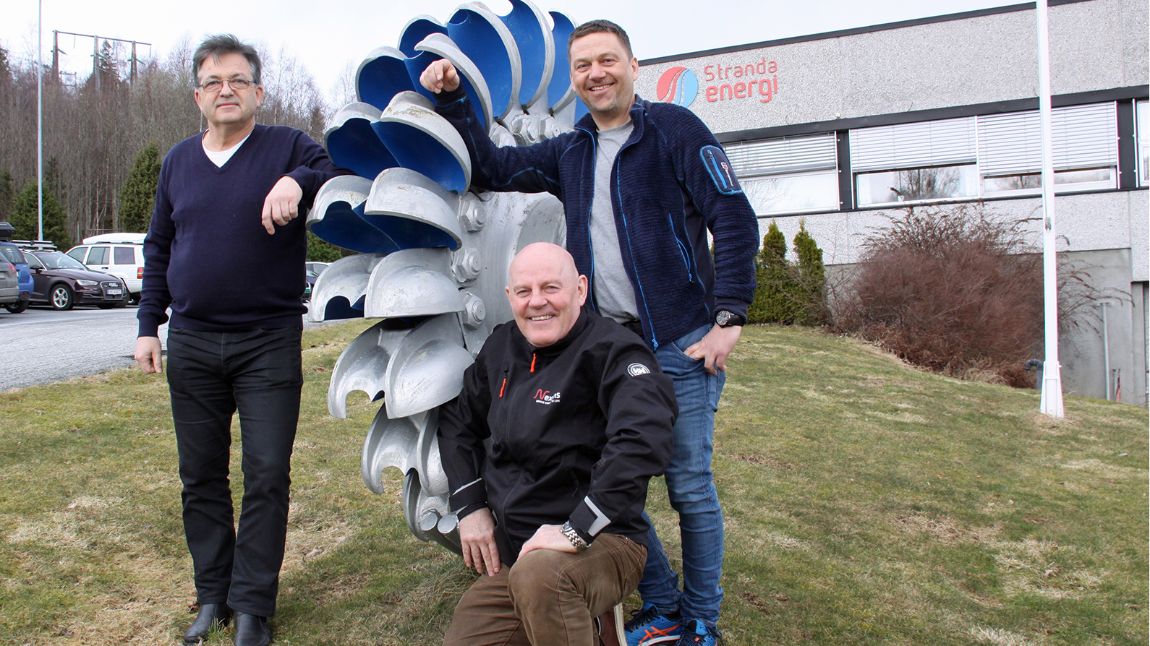
Long lengths
In the tunnel between Stranda and Hellesylt, Stranda Energi had a 160 mm conduit at its disposal. In these areas they laid thick cables to meet the need for backup supply in both directions. The weight – and corresponding friction – of supply lengths of up to 1100 meters of TSLF-OF 24 kV, 3x1x240 mm2 are significant. This friction is substantially reduced by using O-cables, however, and makes pulling them into conduits easier.
“We established a manhole every 500 meters, too. We could lubricate the cable at these points to minimize the challenge of the long stretch,” Remme says.
For this tunnel project, the cost of purchasing the smart cable was ultimately just about the same as purchasing the individual components.
“Reducing the costs of labor, cable-laying, transport and logistics generated the biggest savings,” he says.
Future regulatory requirements
The advantage of establishing fiber between substations is that it puts the cabling systems ahead of future regulatory requirements in terms of communicating with substations. Smart substations and smart grids are rapidly becoming commonplace in power grid companies’ workflows.
“In this context, fiber is a secure way to transfer data, and you never have to think about capacity for the transfer,” says Trond Nesbakken, Regional Manager, Nexans.
Communication between a power station and its individual substations through fiber provides wide scope for use both right now and going forward.
“That’s why it’s smart to include fiber on your pick list when ordering a 24 kV cable,” the Regional Manager says.
Our websites
Select your country to find our products and solutions
-
Africa
- Africa
- Ghana
- Ivory Coast
- Morocco
- North West Africa
- Americas
- Asia
- Europe
- Oceania